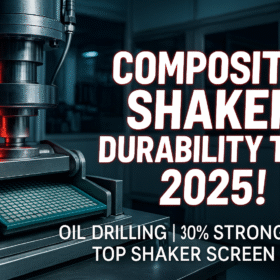
In oil and gas drilling operations, maintaining the quality of drilling fluids is essential for operational efficiency and cost-effectiveness. Shale shaker screens are pivotal in this process, effectively separating solids from drilling fluids to ensure optimal performance.
What Are Shale Shaker Screens? Shale shaker screens are mechanical devices designed to filter out solid particles from drilling fluids. Typically constructed from stainless steel, polyurethane, or composite materials, these screens consist of a wire mesh or filter cloth that vibrates to allow larger particles to pass through, while retaining finer particles. This separation process ensures that the drilling fluid remains clean and reusable, thereby enhancing drilling efficiency and reducing operational costs.
The Importance of High-Quality Shale Shaker Screens: Selecting top-tier shale shaker screens is crucial for several reasons:
Enhanced Solids Control Efficiency: High-quality screens improve the separation of solids from drilling fluids, ensuring that the drilling mud is recovered efficiently and quickly. This reduces the overall cost of drilling operations while minimizing environmental impact.
Protection of Downstream Equipment: By effectively removing large rock cuttings and other solids, shale shaker screens prevent these particles from entering other equipment, reducing the risk of damage and downtime. This helps keep workers safe and minimizes the risk of accidents and injuries on the job.Extended Service Life: Premium screens are designed for durability, offering a longer service life and reducing the frequency of replacements, which contributes to cost savings over time.
Selecting the Optimal Shale Shaker Screen: When choosing a shale shaker screen for your drilling operation, consider the following factors:
Mesh Size: Determines the size of the particles that can be filtered out. Selecting the appropriate mesh size is essential for effective solids separation.
Screen Design: The design affects the screen’s efficiency and durability. Options include flat screens, pyramid screens, and hook strip flat screens, each with distinct advantages.
Material Composition: The materials used in the screen’s construction impact its performance and longevity. Common materials include stainless steel, composite, and polyurethane. Stainless steel screens are durable and resistant to corrosion, making them suitable for harsh drilling conditions.
Conclusion: Investing in high-quality shale shaker screens is a strategic decision that can significantly enhance the efficiency and safety of drilling operations. By carefully selecting screens based on mesh size, design, and material composition, drilling operations can achieve optimal performance, reduce costs, and ensure the safety of personnel and equipment.